Case Study – Why stamping part numbers on add-on parts is the superior strategy
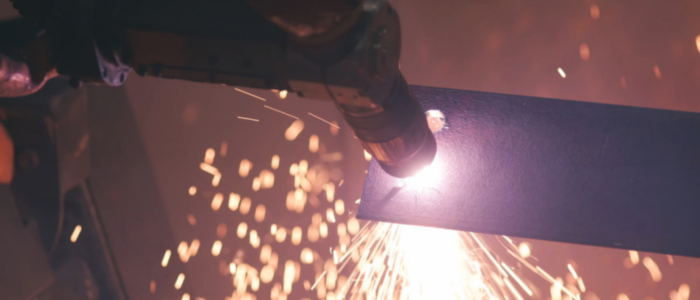
WHY STAMPING PART NUMBERS ON ADD-ON PARTS IS THE SUPERIOR STRATEGY
Has your business ever had a client audit your workshop and ask you to find add-on part number XYZ and then record how long it takes the business to locate this part? What about when a boilermaker/fitter requires an add-on part from a stack of fittings that have not been sorted; how much time is wasted locating these add-on parts? If you want to find a needle in the haystack you need a strong magnet!
SMS has a full range of structural steel add-on part processing machines. These include CNC add-on part plasma cutting with drilling and punching or CNC flat bar punch and shear machines. Both machines from France identify add-on parts using a stamping wheel for the following reasons:
- Every part can be stamped effectively and efficiently compared to laser/plasma scribing or pneumatic marking. Compare the time studies!
- Many parts are supplied to a fabricator with 1 in 10 parts marked. The fabricator as part of the QA/QC process is required to identify every part prior to fabrication that requires hundreds of man-hours per year.
- Parts that have been stamped can be read after
- Processing on an automatic de-burring or edge rounding machine
- Shot blasting before fabrication
- Painting
- Galvanising
- There are limited running costs for stamping add-on parts automatically compared to the gas, power or cutting consumables required for plasma or laser scribing
- Plasma scribing to be effective requires a 30amp torch consumables so a torch needs to be changed from the 160/260/400 amp cutting torch
- Plasma/laser scribing is too slow as the whole bridge needs to move for every character
- Plasma/laser users don’t want to slow the tonnage capacity that can be processed per shift to mark add-on parts so marking is generally performed manually
- Parts are often dirty & wet from the plasma & drilling process so the drilling fluid needs to be removed from each part so the paint marking stays on the part.
- Galvanising companies are only accepting parts marked with a water-based marking pen that react well with the galvanizing process.
SMS will work collaboratively with your business to measure and understand how many man-hours can be re-tasked from your business when stamping add-on parts is deployed instead of alternative methods. The man-hours that are hiding inside your business can be re-tasked to lower the cost per part and man-hours to fabricate. SMS supplies superior machinery strategy so your business can win more and do more, which is what you want, isn’t it? Additional cost and schedule savings can be reviewed on the following case studies and white papers when processing add-on parts on a CNC flat bar machine with the option for automation out-feed part sorting functionality.
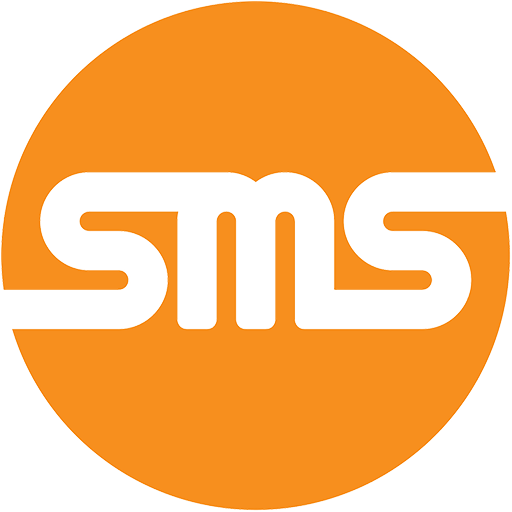
Learn More
Contact Specialist Machinery Sales today to discuss a superior machinery strategy for your business.