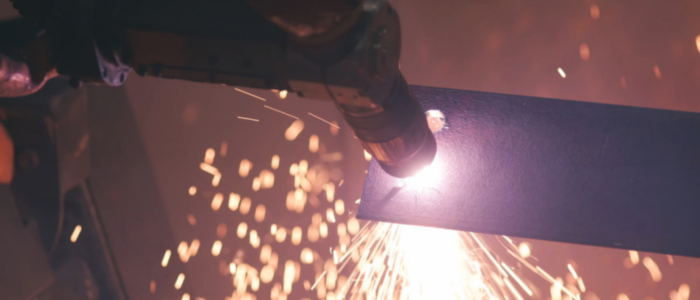
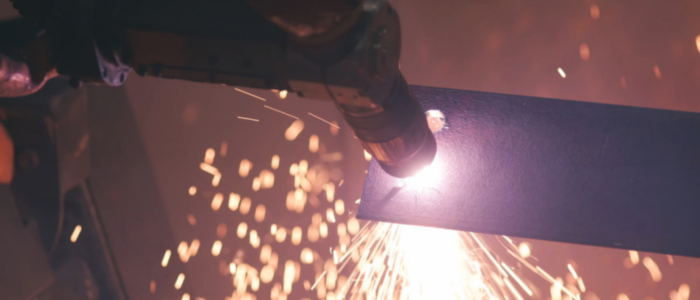
Every fabricator seeks a competitive edge in supply security, cost control, risk reduction, quality, efficiency, and value-added solutions. Investing in the right beamline can deliver this advantage by automating steel processing and layout marking, re-tasking 35 man-hours per 15 tonnes of fabricated steel—translating to significant cost savings and increased output.
Fabricators typically load 15-20 tonnes of fabricated steel per truck daily for site erection. To maintain this pace, a beamline must process at 1.5 tonnes per hour, aligning with the average fitter/welder's fabrication capacity. A workshop with 10 fitters requires the beamline to handle 15 tonnes daily to ensure on-time deliveries within a three-week cycle.
Each fitter spends 10 minutes on an add-on part. With automated layout marking, this is reduced by 5 minutes per part, allowing 50% more fabrication capacity. Across 10 fitters handling 500 add-on parts per shift, this re-tasks 2,500 minutes (or 42 man-hours per shift).
At an hourly rate of $120, this equals $5,040 in recovered labor per shift, or $10,080 per day based on two shifts—significantly improving cost efficiency.
Beyond layout marking, an automated beamline running 100% lights-out re-tasks 10 additional hours per 15 tonnes, increasing overall efficiency. However, this is only possible when the beamline maintains full capacity while V-scoring all four sides of a beam.
A basic beamline that lacks full automation or slows down during layout marking reduces productivity from 24 tonnes per shift to just 6 tonnes—making it impossible to meet project timelines and increasing the risk of site delays.
By re-tasking 35 man-hours per 15 tonnes, fabricators gain:
✔ $4,200 in recovered labor per 15 tonnes
✔ $12,600 saved per 45 tonnes weekly
✔ $655,200 annually (at 15 tonnes per shift, two shifts per day)
Fabricators who automate gain a strategic edge over competitors still relying on basic beamlines that only cut and drill profiles. The ability to re-task 35 man-hours per 15 tonnes allows fabricators to bid more competitively, win higher-margin projects, and increase workshop profitability.
Fabricators focused on security of supply, cost control, reduced risk, and efficiency invest in proven automation solutions rather than outdated beamlines. Forward-thinking workshops dominate the market while their competitors sell off underutilised equipment.
Want to see the numbers for your workshop? Contact us to review a tailored ROI projection.
Contact Specialist Machinery Sales today to discuss a superior machinery strategy for your business.