Case Study – Discover the secrets as to why the market is trending away from automatic percussion marking & moving back to paint marking
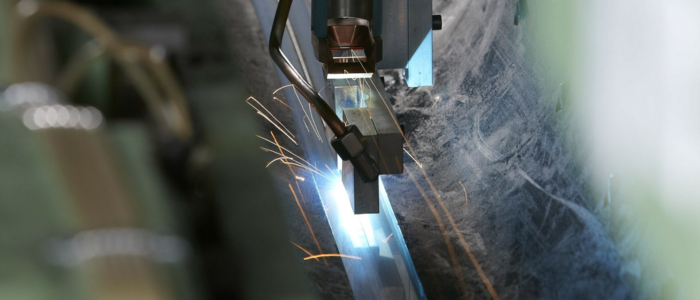
DISCOVER THE SECRETS AS TO WHY THE MARKET IS TRENDING AWAY FROM AUTOMATIC PERCUSSION MARKING AND MOVING BACK TO PAINT MARKING
A recent purchasing decision by a steel processing client ‘Contractor B’ highlights the possible outcomes that result from poorly considered choices. Contractor B sought to purchase a new gantry plasma/drilling machine to address a gap in their product, offering high pressure or flood coolant for drilling. The machine tool builder suggested Contractor B visiting a reference site, this being a fabricator who was using a similar machine for 20 hours a week for in house processing to supply their workshop plasma cut and drilled parts. What was discovered, after advice from Specialist Machinery Sales, and before it was too late, was that the reference site did not mention the following problems as they did not occur in their limited scope of supply?
The reference site normally paints their product offering and was using the older style paint pen to identify parts prior to fabrication that is now not compliant with most galvanising businesses in Australia. If a fabricator requires parts to be galvanised the parts must be identified using a water-based paint marker. The consequence for a business using any plasma cutting machine, with flood or high-pressure coolant, is that every part surface must be dry of the 95% water-based coolant before marking can take place with the appropriate water-based marking pen.
Users of plasma/drilling machines deploying flood coolant or high-pressure coolant on most occasions specified a pneumatic marking device to identify parts. The idea was to avoid manually wiping away the coolant and marking parts with a paint pen. What was found was that the market does not accept the additional costs/time it takes to mark parts deploying the pneumatic marking when the machine can process another full nest of parts in the same time it takes to pneumatically mark parts. Every user of a combination plasma/drill is motivated to increase capacity and improve schedule and costs. The pneumatic marking unit now only meets the performance outcomes of parts that need to be shot blasted first prior to fabrication.
2016 clients of SMS will not need to wipe coolant from parts prior to marking with a paint pen due to the minimal coolant that is delivered to the end of the drilling tip. The MQL is a state of the art method of providing atomised lubricant combined with high-pressure air through the spindle and the tool departing at the cutting tip. The lubricant is supplied at less than 50 millilitres/hour while the air at 100 psi and flows up to 1,500 litres/minute blasts swarf out of the hole.
The same applies when investing in a wet bed water table. The top of the plate is no longer is submerged in fluid from the cutting table and the same lubricant and high-pressure air is used instead of flood and high-pressure coolant. Imagine how many parts are processed each year and the number of parts that need to be wiped clean and dry before paint marking takes place.
We all look at developing our business. Fabricators who place orders with steel service centres do so with the supplier that marks plates accurately and uses the latest standard water-based paint marking pen that is compatible with any galvanising quality procedure. A structural steel fabricator purchasing 450 tonnes of add on parts per year may have two full-time staff sorting these from their internal or external plasma cutting machines. Schedule and costs can be improved when adding on parts can be identified effectively and efficiently.
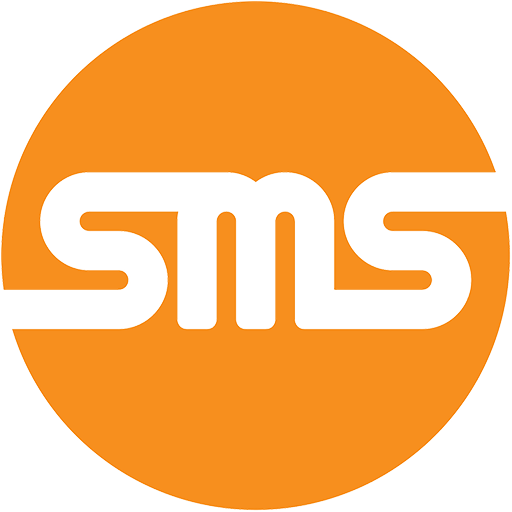
Learn More
Contact Specialist Machinery Sales today to discuss a superior machinery strategy for your business.