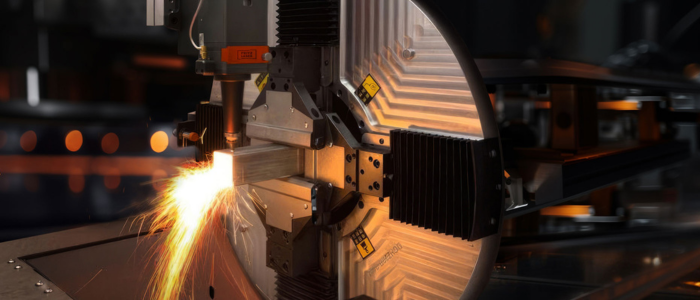
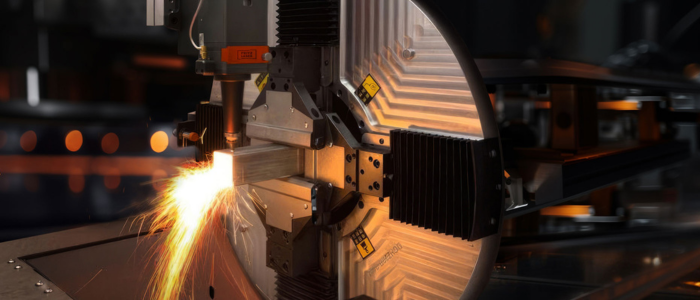
Buyers of plasma cutting machines consider investing in a cutting table that requires minimal floor space. Many machines are designed to have one sheet on the cutting table then removing the cut pieces and skeleton before loading the next sheet. What is discovered with this style of plasma cutting machine is the torch arc on time is decreased by 50% due to the material handling implications of not having a longer or wider machine.
For example, customers with a longer or wider machine can be cutting parts on zone A and at the same time can be unloading cut parts and the skeleton or remanent on zone B. Once this process is completed a new plate can be positioned in zone B and be ready for processing when the cutting is being completed in zone A. That is why we recommend a longer or wider cutting bed that provides flexibility in the side plates that can be loaded onto the cutting table. The operator can position plates ready to be processed in multiple cutting zones on the plasma cutting table whilst the plasma torch is in operation. This increases the arc on time which improves capacity, schedule and cost.
Another trend with steel services centres and fabricators is having a wider plasma cutting table so 6m or 9m long plates can be loaded perpendicular to the X-axis.
This allows the company to keep various popular size plates on the cutting table to reduce the material handling time and always have full-size plates to cut from to improve the cost and schedule.
Review the following case studies that reflect good choices your peers have made:
Inviting Specialist Machinery Sales to participate in the design and specification of your cutting table will reduce material handling times and improve arc on efficiency.
A correctly specified cutting table provides a competitive advantage to your bid for supplying a price and delivery sensitive product to the market.
Contact Specialist Machinery Sales today to discuss a superior machinery strategy for your business.