Case Study – You are not alone in specifying a CNC controller & PLC that has built in redundancy
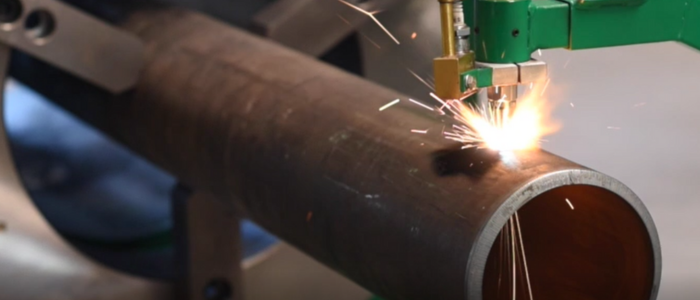
AVOID COSTLY MISTAKES THAT AFFECT BID WIN DRILLING CONTRACTS AND ROI
We have all seen the speed at which technology and innovation can transform an industry, like the mobile telephone which we all now use and rely on. Most mobile phone users at the start of the century were delighted to be using a Nokia, who are now no longer trading. In a short period of time, the number one selling phone brand was left behind as the smartphone allowed the user to upgrade to the latest functionality and applications without changing the handset. The same can be true with the CNC controller and PLC that is specified on a plasma cutting machine.
Ensure your business has the PLC and CNC controller just like the smartphone has the flexibility built into the design for upgrading additional features, without having to replace the machine. Nokia is now relegated to the history books because their handsets had to be replaced if new and smarter applications were required from the user.
Most businesses investing in a plasma cutting machine do not consider the CNC controller or PLC and how the functionality of the ‘brain’ of the machine can become uncompetitive. These plasma cutting machines are forced into early retirement because the CNC controller and PLC technology become redundant.
For decades, plasma cut parts have been a price and delivery sensitive product. A plasma cutting machine’s specification must have the flexibility to meet or exceed the performance outcomes that the market requires. What is discovered, once it is too late, is that many plasma cutting machines have redundancy designed into the PLC and CNC controller so any future upgrades to the specification are not possible. The contract plasma cutting market has limited loyalty and will place orders with suppliers that have machine specifications that can meet their performance outcomes.
When investing in a gantry style plasma cutting machine with drilling and extra machining capacity there are advantages of specifying a soft PLC and a Burny CNC controller. Clients of SMS understand the flexibility that any Electrical Engineer can access the Soft PLC along with the Burny CNC control that is integrated together so the parameter settings can be accessed easily. The advantage of this flexibility is when a business wants to increase functionality to the machine the upgrade is possible without contacting the machine tool builder. This ensures the machine tool doesn’t need replacing or the technology becomes redundant. This is a contrast to the choice of a specification with the CNC and PLC being two separate physical devices where the machine tool builder captures your service and upgrades as they will be reluctant to share the intellectual property for the CNC controller and PLC settings. Client’s don’t need to upgrade to the latest machine which is great for the machine tool builder if they can keep their current fleet of machines effective and productive.
Having the most up to date CNC controller at all times will ensure that the machine will not be left behind the technology curve and will continue to provide a competitive cost and schedule to the market. Clients of Specialist Machinery Sales appreciate not having to relegate plasma cutting machines to low tolerance or low margin work when the CNC controller can remain relevant and up to date.
Plasma cutting and drilling machines with extra machining capacity are like formula one cars for motor vehicles in regards to introducing the latest technology and innovation. Clients appreciate when additional functionality can be included on the chassis of the plasma cutting machine with drilling and extra machining capacity the CNC controller and PLC can accommodate the upgrade. This avoids the business having to trade out of the current model machine to remain competitive with the latest technology.
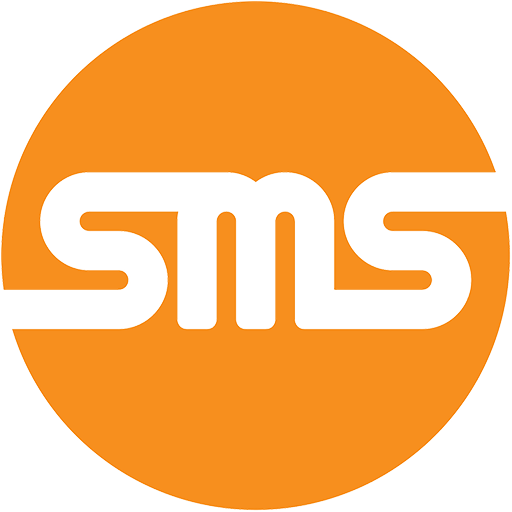
Learn More
Contact Specialist Machinery Sales today to discuss a superior machinery strategy for your business.